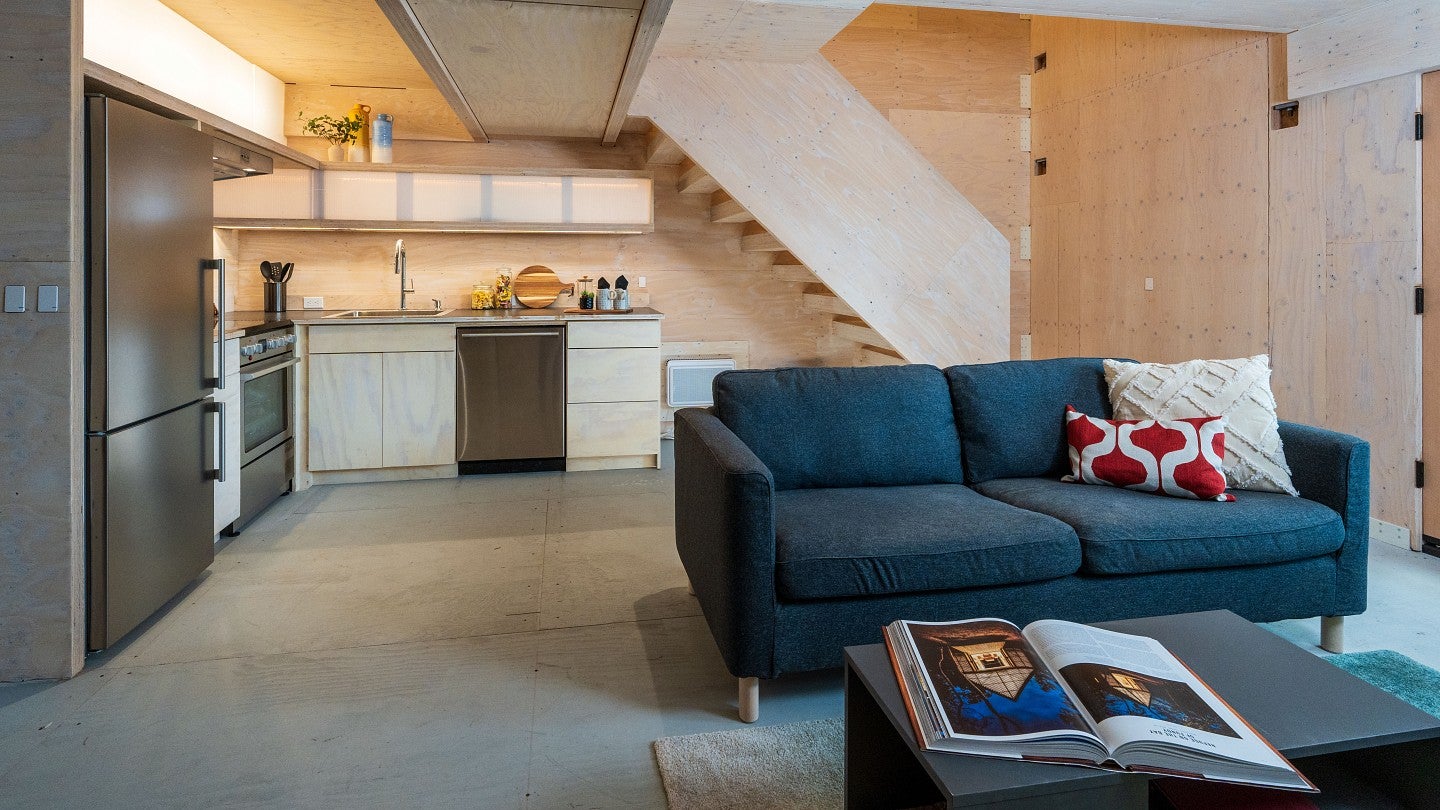
Test home heralds innovative, greener construction method
UO and OSU partner on solutions to help with housing crisis, wildfires and economy
In the future, your new home might be delivered by flatpack like an IKEA bookshelf. Instead of a frame of two-by-fours, workers would assemble prefabricated panels that fit together like pieces of a gingerbread house — only much more precisely.
A University of Oregon research and design team has completed construction on a prototype for such a house. They hope it’s a step toward sustainable, efficient and faster alternatives to traditional home construction.
Researchers with the TallWood Design Institute, a collaboration of the UO and Oregon State University, spent two years designing and building the 760-square-foot house made from mass plywood panels manufactured in Oregon by Freres Engineered Wood.
A UO research and design team built the prototype home inside OSU’s AA “Red” Emmerson Advanced Wood Products Lab.
So far, the small house is making a big impression.
The test home demonstrates a new construction model that could help with housing shortages, the economy and wildfire mitigation, said Judith Sheine, a UO professor of architecture and the institute’s director of design who led the project with assistant professor of architecture Mark Fretz.
Sheine hopes the project will encourage architects and builders to consider mass timber, the products made from cross-laminated layers of veneer or lumber that the institute researches and tests, for prefabricated housing.
This first prototype marks a big step forward, Sheine said. The mass plywood home could represent a new solution to help address Oregon’s housing crisis, especially affordable options known as middle or workforce housing.
“Visitors have been enthusiastic about the prototype, and several have asked how they can get one,” Sheine said. “Hopefully this will lead to the production of prefabricated mass timber housing in Oregon.”
UO faculty and students constructed the two-bedroom, 1½-bathroom home inside the A.A. “Red” Emmerson Advanced Wood Products Laboratory at OSU, working with lab staff members. A founding member of the Oregon Mass Timber Coalition, the institute received a portion of the $41.4 million awarded by the U.S. Economic Development Administration’s Build Back Better Regional Challenge in 2022. The prototyping project was one of nine funded by the award. That federal support, along with ongoing funding from the state of Oregon, allows the institute to drive mass timber research and development, contributing to sustainable housing and resilient forestry initiatives.
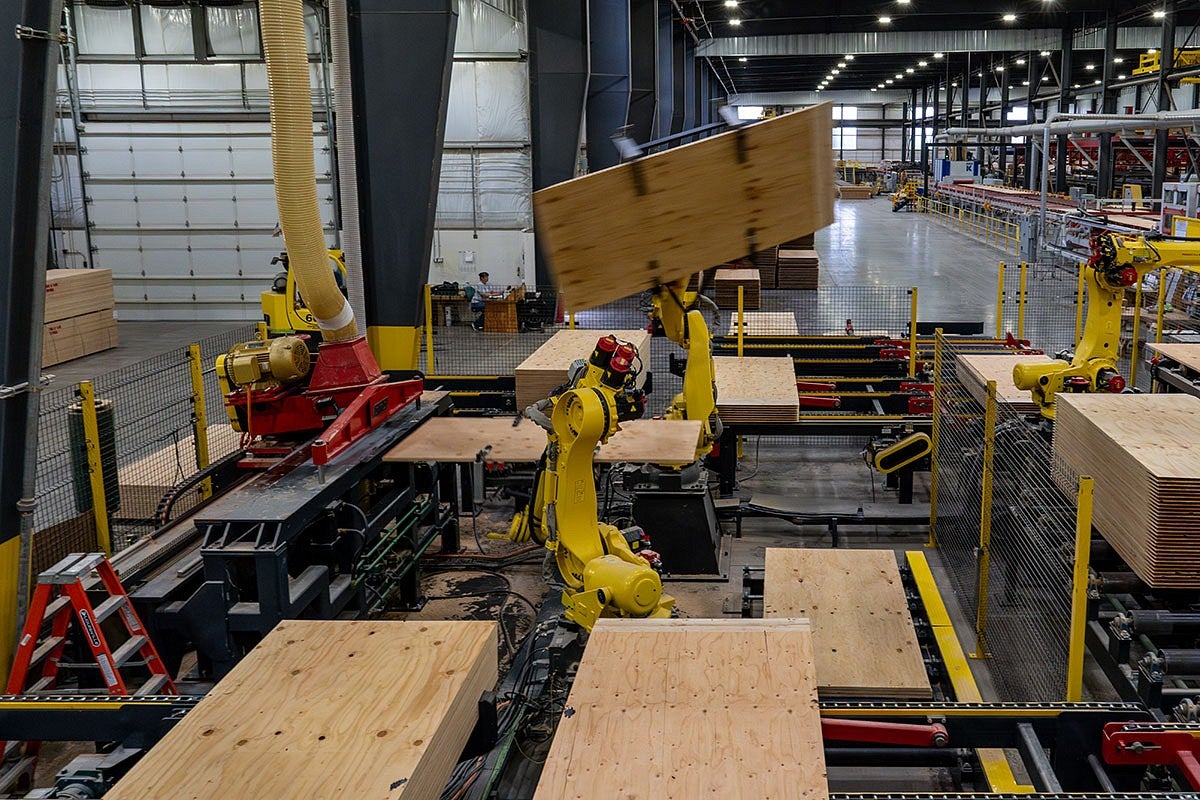
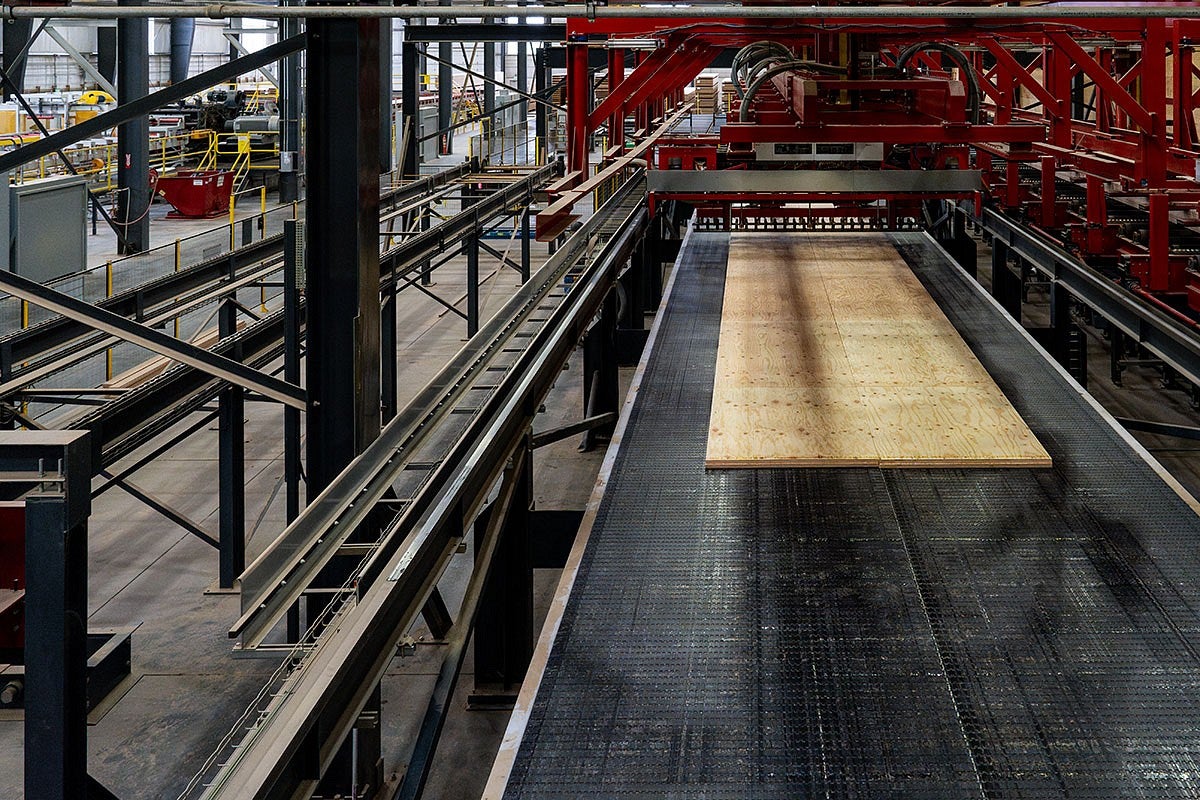
Designing for the future
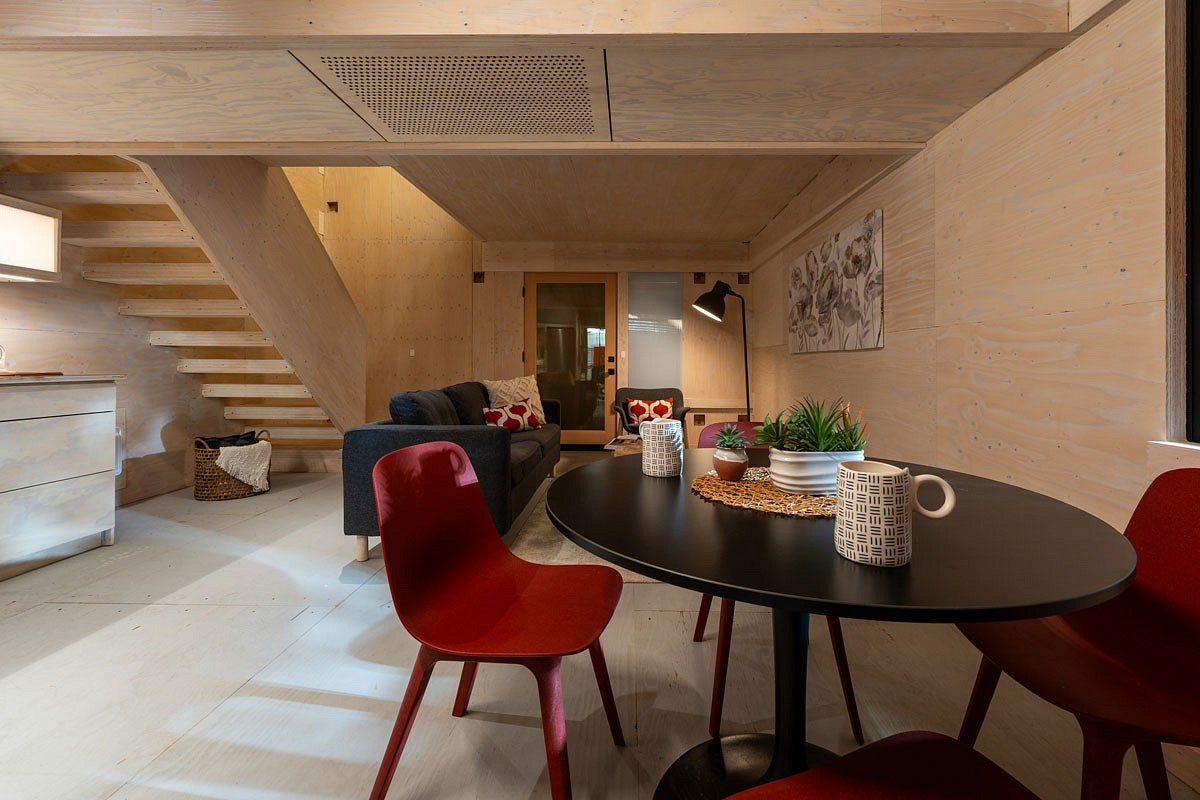
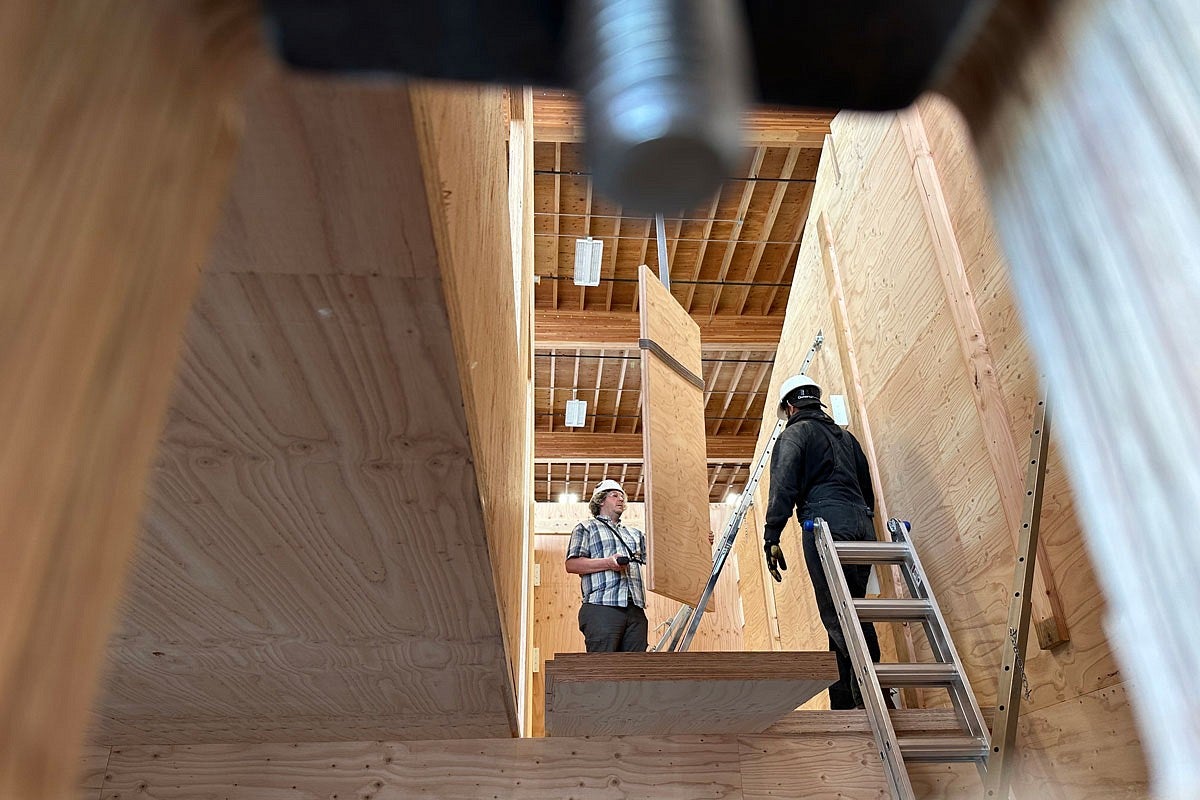
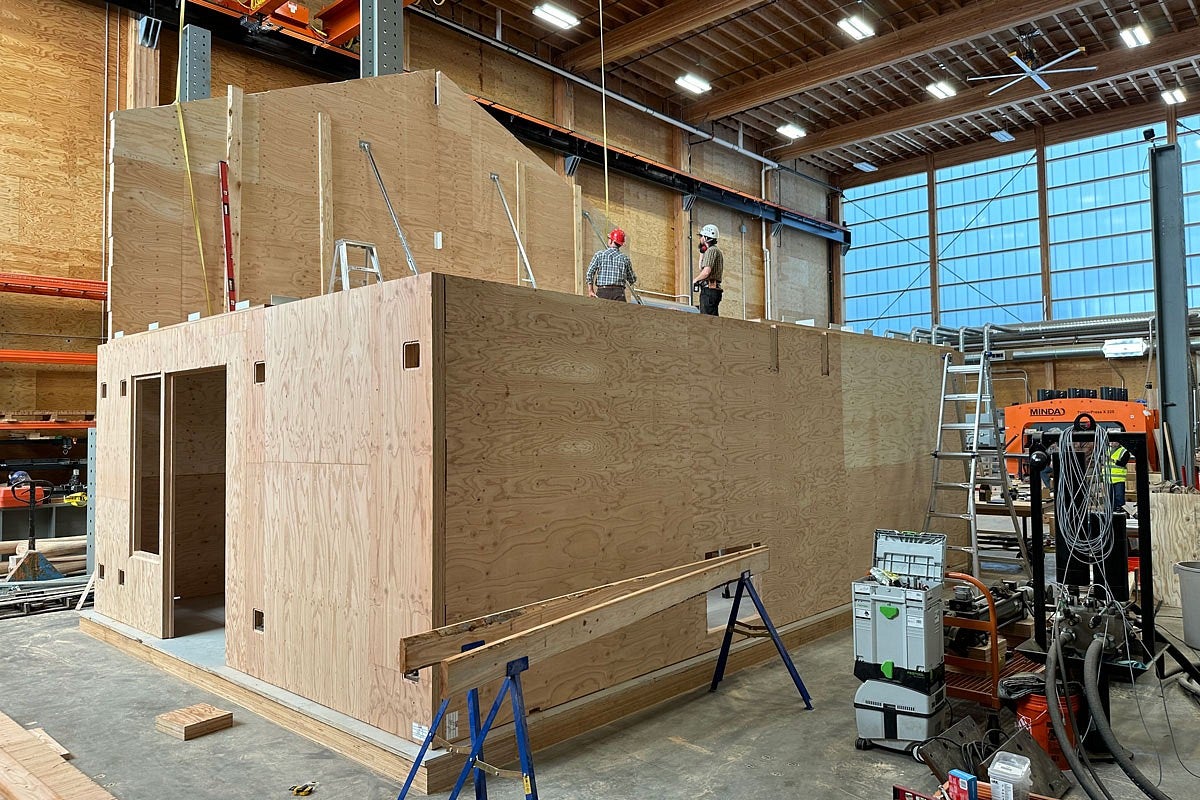
Fretz, co-director of the UO’s Institute for Health in the Built Environment, led the crew that built the house.
“A computer model is one thing,” Fretz said. “But now you can walk through it and experience a new kind of house and a working concept for housing in Oregon.”
Comfortable, light and replete with exposed wood, the mass plywood panel home has become a popular place for people working in the lab to share lunch, meet and conduct Zoom calls.
Throughout the building process, Fretz’s team tested construction techniques, tweaked the design and made new discoveries. Developing a full-size version has been invaluable. For instance, the team was initially concerned that extensive natural wood might be aesthetically overwhelming. It’s not.
Working with a full-size model also helped them try out ideas for lighting, electricity, windows and more.
The panels were manufactured by Freres Engineered Wood in Lyons, a small town east of Salem, then fabricated in the Emmerson Lab using a computer numerical-controlled machine that cut the mass plywood panels into predesigned shapes.
The institute helped Freres develop the new product, which is manufactured with a one-eighth inch tolerance — much more precise than conventional home construction.
Fretz was curious to see if that precision would be a challenge, but fitting the pieces together was surprisingly fast and easy. Pressurization testing revealed that the tight-fitting panels reduced drafts, making the house energy efficient.
It’s also efficient with space. The interior panels are 2 inches wide, whereas a typical stud frame wall is more than twice that. There’s more room inside than the exterior might suggest.
The house is more fire resistant than a conventional wood house and is designed to be seismically resilient.
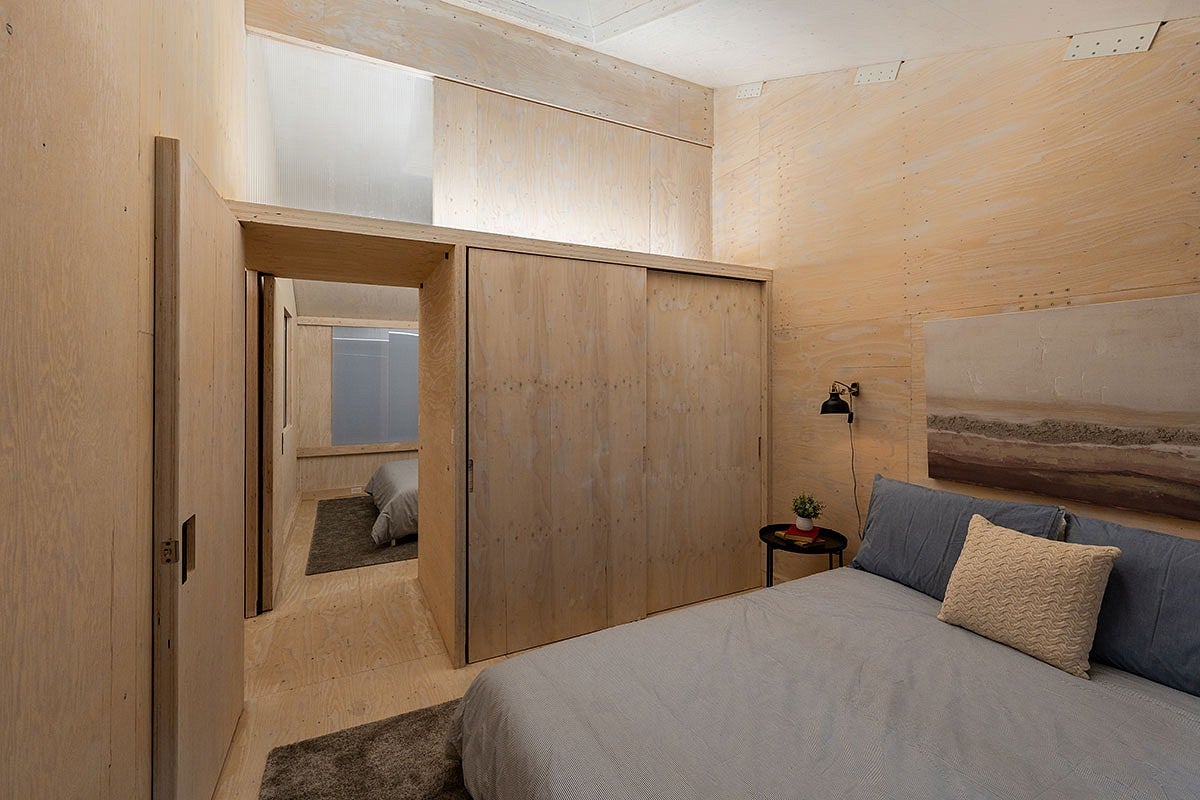
Sustainable materials, sustainable economy
Mass timber construction emerged in Europe in the mid-1990s and is becoming more common in the U.S., but so far it’s used mostly for larger buildings typically made with concrete or steel frames. Mass timber is stronger per pound than steel and concrete, which have bigger carbon footprints.
Mass timber construction offers more sustainability benefits. Wood sequesters carbon that could otherwise end up in the atmosphere. And the panels require no drywall, another carbon culprit.
Veneer products can use approximately 70 percent of the wood in a log, as opposed to the typical 50 percent used for dimensional lumber. Mass timber also can be precisely designed and prefabricated so that the panels are used efficiently, with minimal waste.
Despite these efficiencies, cross-laminated timber, the most common type of mass timber panel, has proven too expensive for homes when compared to traditional light-frame construction. But the new institute’s prototype house may challenge that.
Because they use less fiber than a standard cross-laminated timber panel, Freres’ thinner panels are more cost-effective. If the new model takes off, automation and efficiencies of scale will drive costs down, Fretz said. Just-in-time delivery also will eliminate the extensive lumber inventories required by traditional construction supply chains.
Institute researchers hope the new building products also will transform how Northwest forests are managed because mass timber houses can be produced with small-diameter logs removed to reduce wildfire. Freres’ mass plywood facility can use logs with tops as small as 5 inches in diameter.
Accurate sourcing could promote more sustainable forestry, as with the new 9-acre mass timber roof in Portland’s airport made from trees harvested within a 300-mile radius.
In addition to forestry jobs, a growing mass timber industry would create skilled manufacturing jobs, boosting both rural and urban communities.
As they show off their model home, institute researchers already have begun work on a second prototype to be built outside the lab. The outdoor version will include insulation and cladding and enable thermal and acoustic testing.
A contractor will build version 2.0, which will help the team develop more accurate estimates of construction costs and streamline the process based on input from construction professionals.
As the design details are optimized, the Oregon Department of Land Conservation and Development has been working with Oregon cities to update zoning codes to accommodate the novel approach. Eventually, the home designs will be available free to the public.
For those wondering when they can move into a mass plywood-panel home, the project team is working on version 3.0, a pilot project in Burns. Working with the nonprofit Regional Rural Revitalization, they’re planning a four-unit cottage cluster.
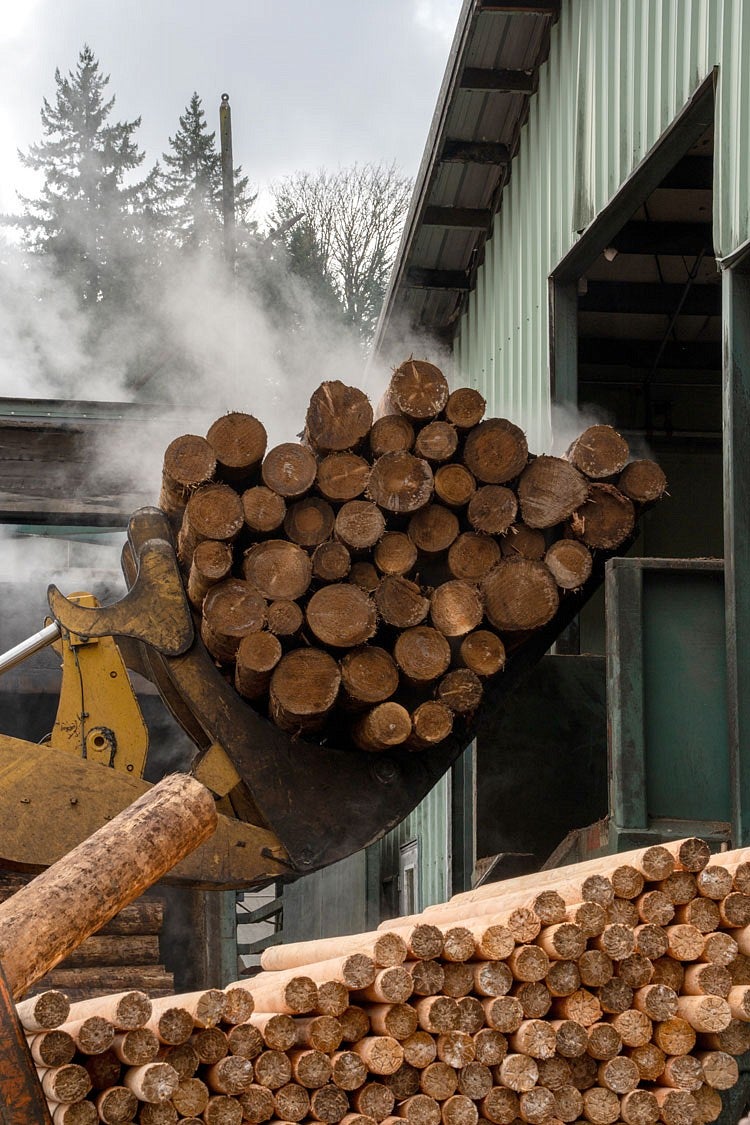
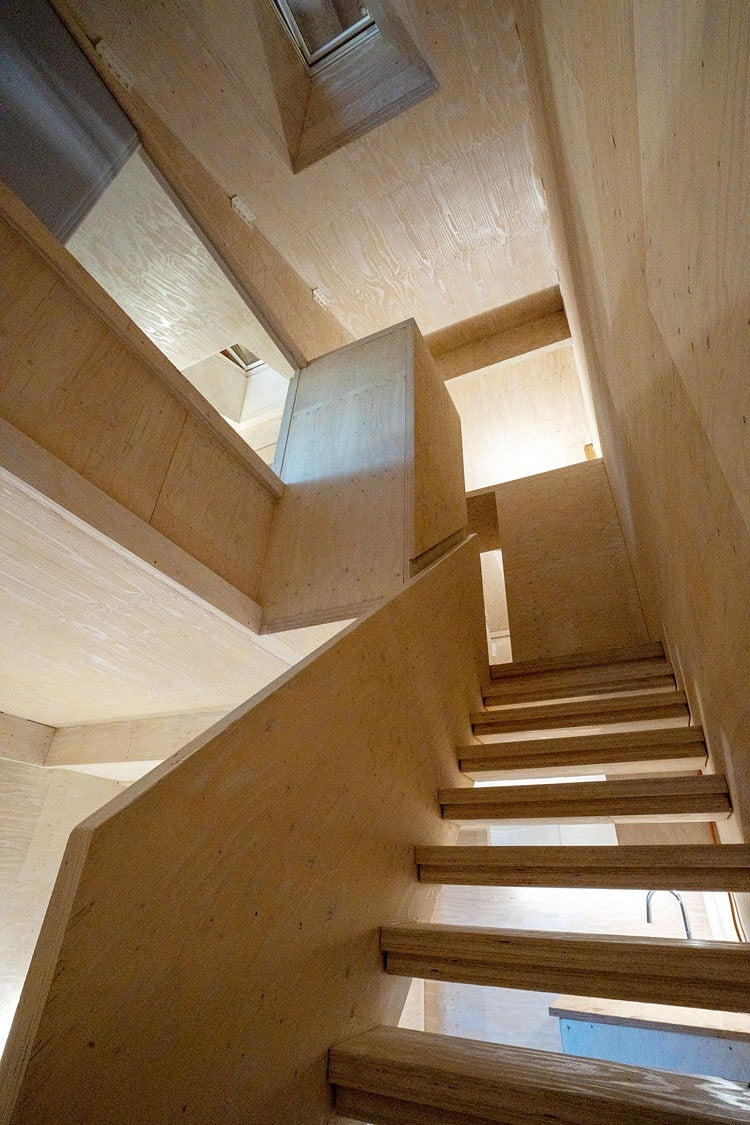
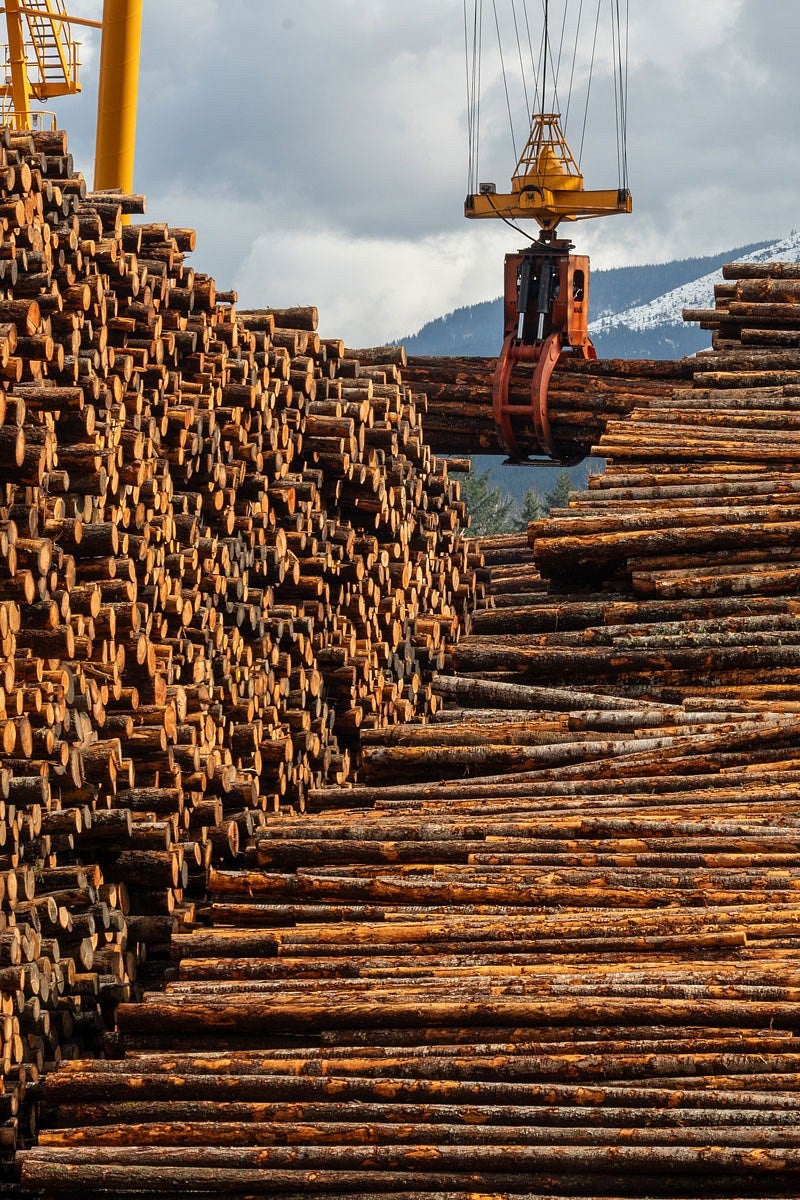
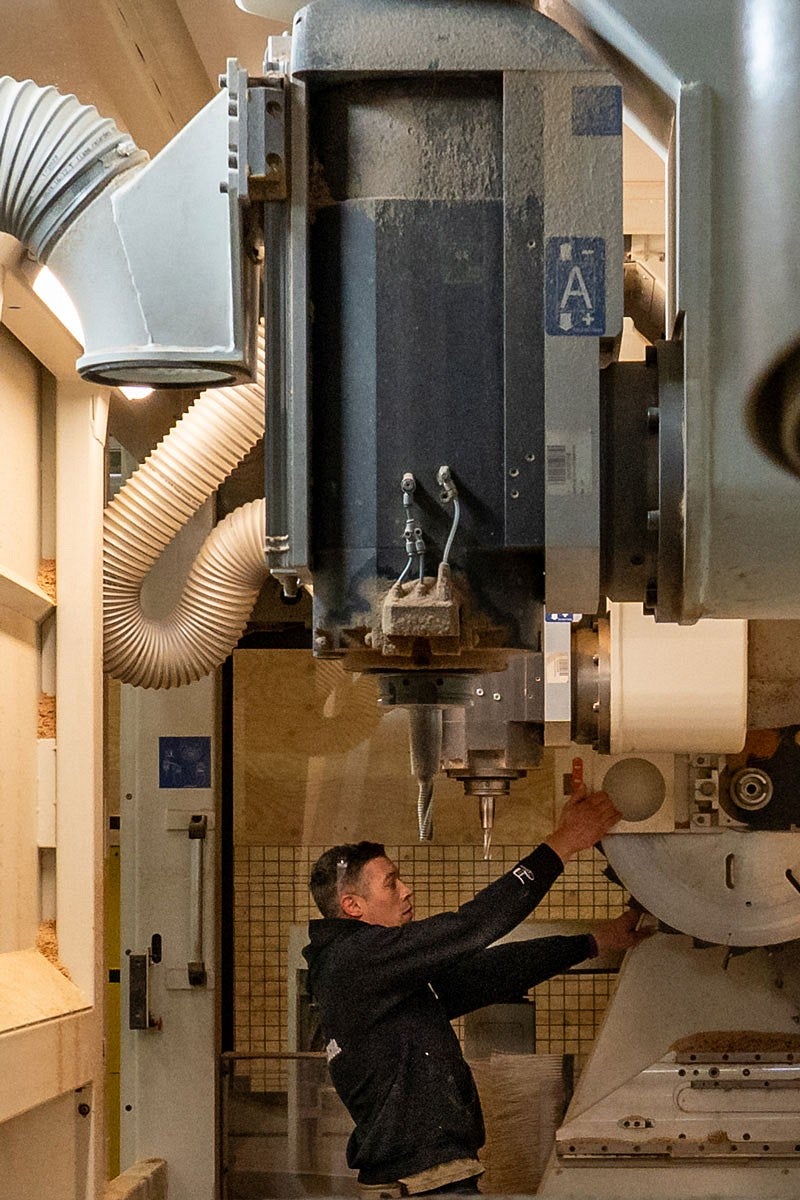
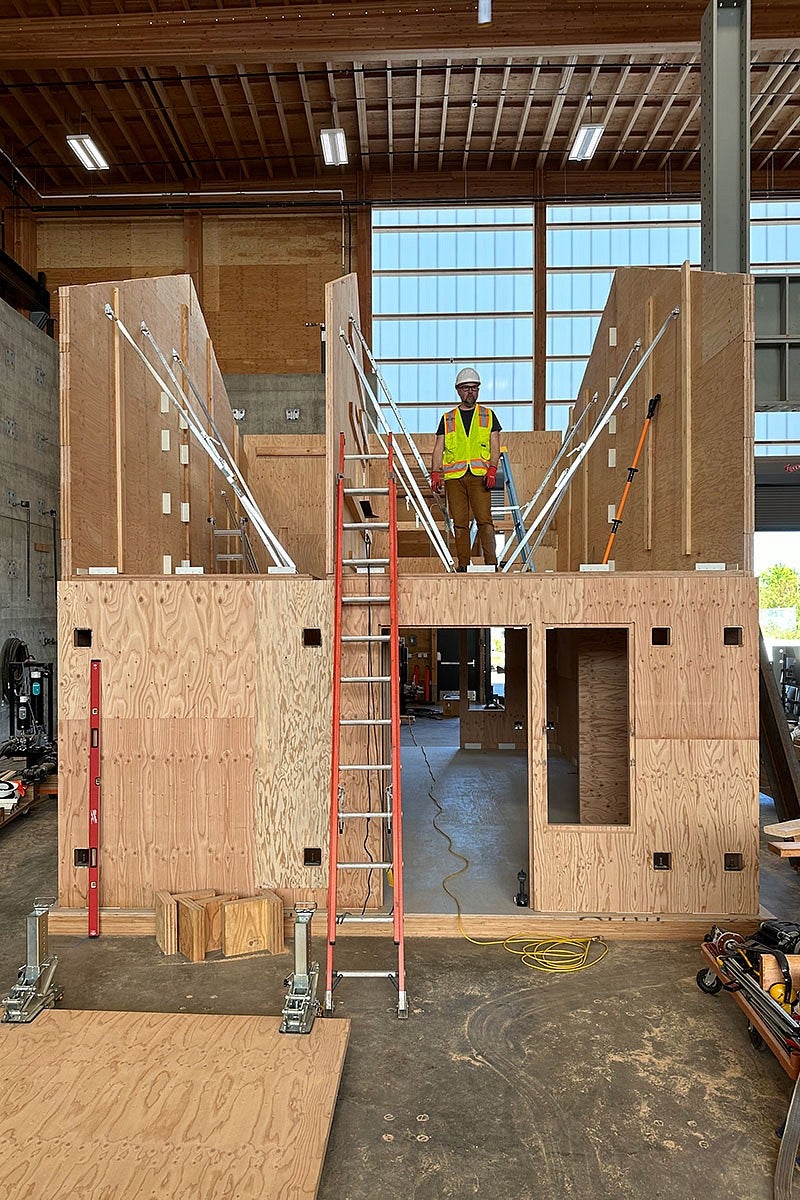